Contact Us
+86 13480709275
Block 11,Shunchang Industrial Park, Xiaobian Second Industrial Zone, Chang'an Town, Dongguan City, China
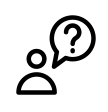
How Can We Help?
If You Need Any Helps Please Feel Free To
customized sintered powder metal components powdered metal metallurgy parts
Harber Industrial Ltd is a leading manufacturer of Metal Injection Molding Products, Powder Metallurgy Parts and precision metal parts that other conventional processing produce.We have developed more than 2000 different mim metal components for these applications alone. Our offering includes variety of materials with different properties such as high strength, wear resistance, corrosion resistance etc. In recent times with increase in automation across the industry, usage of MIM components becoming more popular & familiar. Our experience in serving this segment for a long time gives us immense advantage to understand specific requirement, and provide cost-effective quality solutions accordingly.
- Product Details
- Company Profile
- Packaging&Shipping
- Ordering Steps
Custom Made Stainless Steel Powder Metallurgy Sintered Parts
Materials: | /Brass/Carbon Steel/Aluminum/Stainless Steel: 17-4PH, 304L ,316L , 420J2, 440C.etc. |
Iron nickel alloy: | Fe-8%Ni |
Tool steels: | SKD 11,4141 |
Finish: | Polishing Or As Your Demands. |
Applications: | Precision Instrument,Medical Device,Fishing Gear Accessories,Automobile Parts,Pneumatic Power Tool.etc. |
Processing: | Mixing, Pelleting, Injection, De-Binding, Sintering, CNC Post Processes. |
Payment: | 50% Deposit,50% Before Delivery By T/T |
We can do: | a: CNC turning parts;+/- 0.01mm precision parts;machining parts;coating parts;miling parts; powder metallurgy parts; cusotmized make parts; MIM parts; b: metal parts; stainless steel parts; brass parts; aluminum parts; pom parts; c: gear parts; bevel gear parts; ring parts; rack parts; pin parts;
D: Arrow head parts; broadheads; hunting arrow heads; watch cases; watch parts; fishing parts; phone parts; camera parts; medical device parts.etc. |
Equipment advantages:
Mixing machine, Injection molding machines, Degreasing furnaces, Vacuum sintering furnace; Automatic pressing machine, Repressing machine, CNC machining equipment, finishing machining machine, polishing machine, Automatic oil punching machine and so on...
Testing equipment:
Projector, Salt spray test machine, Partial pendulum instrument, electronic balance, electronic gravity apparatus, universal tester, Rockwell hardness tester, Density tester, gauge block, dial indicator, micrometer, Vernier.
What's the MIM technology and its advantages and features.
Simple to Complex Designs
A multitude of design capabilities as there is no extra cost for unlimited features or markings, precision complex net-shape components from a variety of compositions
Metal Variety
Suitable for almost any type of metal, it can use all kind of metal material(such as stainless steel, iron, ceramic and titanium, etc)
Low Tolerances
Metal injection molding can maintain low overall dimensional and locational tolerances
Quick Prototyping
Quick turnaround on short runs. Compound tooling can combine more than one prototype with the same material
Low Cost Modifiable Tooling
Produced quickly and low-cost revisions, MIM injection molding can produce precise part geometry without cutting and secondary processing. It can produce high-density and highly complex structural parts and reduce costs for the whole production. its finished products is close to final products, reducing the post-treatment cost, and then save production cost
Intact Metal Properties
The density of structural parts varies greatly. The friction between PM powder and tools will make the parts uneven. The MIM injection molded parts are uniform in all directions, and the relative density can reach 95% - 99%. The sintering temperature of MIM is much higher than that of PM, the strength, toughness and wear resistance of MIM injection molding are significantly higher, and the utilization of raw materials is high.
compared with tranditional CNC and precision casting process, the structure are more even and preformance is much better
compared with PM(Powder Metallurgy), MIM can produce more complex shape and better preformance metal products.
Environmentally Responsible
The metal injection molding solution (raw materials) is recyclable, safe to use, and can be reused for future metal molding
Production cost comparision between MIM and other processes
Cost Effective Design Flexibility/ Material Variety and Integrity
Powder metallurgy can ensure the accuracy and uniformity of the material composition ratio. Suitable for producing products of the same shape and large quantities, low production cost.
Compare with other process
Parameter | MIM | CONVENTIONAL PM | MACHINING | INVESTMENT CASTING |
Density | 98% | 88% | 100% | 98% |
Tensile Strength | High | Low | High | High |
Elongation | High | Low | High | High |
Hardness | High | Low | High | High |
Min. Wall Thickness | 0.5 mm | 1 mm | 0.5 mm | 2 mm |
Complexity | High | Low | High | Medium |
Surface Finish | High | Medium | High | Medium |
Production Volumes | High | High | Low | Medium |
Range of Materials | High | High | High | Medium-High |
Cost | Medium | Low | High | Medium |
Service:
1, 100% inspection before shipment.
2, Satisfied packing, carton, wooden case, pallet,or according to your requirement.
3, Samples are within 35-40 days after the receipt of the deposit. production will be finished about 25-30days after samples confirma
Production Capacity comparision of MIM and other process
Most difficult metals and compounds, pseudo alloys, porous materials can only be manufactured by powder metallurgy
MIM material
Material | Composition |
Low alloy steel | Fe-2Ni, Fe-8Ni |
Stainless steel | 316L, 17-4-PH |
Tool steel | 42CrMo4, M2, Skd-11, C45 |
Carbide | WC-Co(6%) |
Ceramics | Al203, ZrO2, SiO2 |
Tungsten alloy | W-Ni-Fe, W-Ni-Cu, W-Cu |