Contact Us
+86 13480709275
Block 11,Shunchang Industrial Park, Xiaobian Second Industrial Zone, Chang'an Town, Dongguan City, China
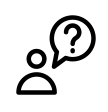
How Can We Help?
If You Need Any Helps Please Feel Free To
Sewing Machine Presser Foot MIM Parts
- Product Details
- Company Profile
- Packaging&Shipping
- Ordering Steps
Presser foot sewing machine parts and sewing accessories are essential for any sewing project. These parts and accessories help to ensure that your sewing machine is functioning properly and that you have the tools you need to complete your project.
MIM metal products are used for various forms of presser feet, presser foot assemblies, base plates, etc., which are used in sewing machines to withstand the abrasion of sewing threads, needles, and the object being sewn, as well as the stress of processing.
Due to the continuous friction with the surface of the tool, the hardness and abrasion resistance of the tool material is severely tested, and if the thread color is light, there is also the concern that the friction sheds the surface material of the tool, resulting in rust stains and discoloration of the sewing thread.
Sewing Machine Presser Foot MIM Parts Characteristic
The MIM presser foot is the part of the sewing machine that holds the fabric in place while you sew. There are different types of presser feet available for different types of sewing projects.
Material: Presser feet are typically made of metal, such as stainless steel or zinc alloy, to provide durability and stability during sewing.
Shape: Presser feet come in different shapes and designs to accommodate various sewing techniques and fabric types. Some common shapes include standard presser feet, zipper presser feet, buttonhole presser feet, and blind hem presser feet.
Non-stick coating: Some presser feet have a non-stick coating, such as Teflon, to help glide smoothly over sticky or difficult fabrics like leather or vinyl.
Many MIM products are used as mechanical parts of sewing equipment.
Design elements of MIM sewing and embroidery machine parts
As a result, there are several strict requirements for sewing and embroidery tool materials:
The material texture must be hard and wear-resistant, and is required to be able to have at least HRC 40 degrees;
Due to the continuous friction of the sewing thread, the surface of the material must not chip off and cause rusting of the sewing thread, and the integrated design of the parts will contribute to the strength and cleanliness of the tools;
Able to conduct heat quickly to dissipate the heat caused by the friction of the sewing thread to avoid possible melting of the sewing thread;
Dimensional tolerances of parts and assemblies;
Due to the high wear and tear, it must be frequently disassembled and replaced, the price of the parts should be affordable, and the damaged products should be recyclable to reduce the burden on the environment;
The manufacturing process of the sewing tool should have a special design of the guiding surface so that the sewing thread can be smoothly discharged.
For sewing and embroidery process, the use of MIM process can simplify the design of parts, and avoid casting voids, welding defects, by heat treatment and tempering to enhance the life of the parts, and the use of injection molding to a large number of manufacturing in order to save costs, in particular, the MIM has a plastic injection of beautiful surfaces can be in line with the parts part of the special features to assist the emergence of the thread of the sewing thread smoothly and other advantages, has been the other processes, including casting, die-casting, sheet metal stamping, and the use of MIM, the MIM process can be used in the manufacture of sewing tools. MIM process in sewing and embroidery machine MIM parts will be solid and irreplaceable, this is a MIM completely replaced by the industrial field.
Applicable Industries | Manufacturing Plant, Machinery Repair Shops, Construction works , Energy & Mining, Advertising Company |
Weight (KG) | 0.63 KG |
After Warranty Service | Video technical support, Online support |
Machinery Test Report | Provided |
Place of Origin | Guangdong, China |
Surface treatment | Chrome plating |
Technology | Metal Powder Injection Molding(MIM) |
Package | Tray and carton |
Tolerance | Generally 0.05mm |
Equipment advantages:
Mixing machine,Injection molding machines,Degreasing furnaces,Vacuum sintering furnace;Automatic pressing machine,,Repressing machine,CNC machining equipment,finishing machining machine,polishing machine,Automatic oil punching machine and so on...
Testing equipment:
Projector,Salt spray test machine,Partial pendulum instrument,electronic balance,electronic gravity apparatus,universal tester,Rockwell hardness tester,Density tester,gauge block,dial indicator,micrometer,Vernier.
What's the MIM technology and its advantages and features.
MIM is an advanced metal forming technology that use injection molding machine to manufacturing precision and complex metal parts, which combines the advantage of PM and plastic injection molding.
It's suit to do mass production with complicated shapes, create metal parts with complex geometries; MIM technology can accurately produce components features such as internal and external threads, undercuts, teeth (e.g., gear teeth), slots, holes, fins, markings, and engravings.
MIM process imposes few restrictions on the part design. It gives freedom to manufacture a variety of shapes, can fabricate multi-component parts as a single piece
Wide selection of metal materials for MIM, It can use all kind of metal material(such as stainless steel, carbon steel, copper alloys, nickel alloys, tungsten alloys, cobalt alloys, iron, carbide, ceramic and titanium, etc)
Its relative density can achieve more than 98%, MIM parts are produced with high density, resulting in excellent mechanical properties, including strength and hardness. This makes MIM a great solution for components that need to withstand high stress and wear.
Its finished products is close to final products, less material wastes and scrap than a machining process, which is important for expensive materials such as refractory materials, titanium alloys, superalloys, and specialty metals. reducing the post-treatment cost, and then save production cost.
Compared with tranditional CNC and precision casting process, the structure are more even and preformance is much better, Consistent part quality, Consistent part density & strength
Compared with PM(Powder Metallurgy), MIM can produce more complex shape and better preformance metal products.
Production cost comparision between MIM and other processes
Cost Effective Design Flexibility/ Material Variety and Integrity
Powder metallurgy can ensure the accuracy and uniformity of the material composition ratio. Suitable for producing products of the same shape and large quantities, low production cost.
Machinery Structural Parts Manufacture Compare with other process
Parameter | MIM | CONVENTIONAL PM | MACHINING | INVESTMENT CASTING |
Density | 98% | 88% | 100% | 98% |
Tensile Strength | High | Low | High | High |
Elongation | High | Low | High | High |
Hardness | High | Low | High | High |
Min. Wall Thickness | 0.5 mm | 1 mm | 0.5 mm | 2 mm |
Complexity | High | Low | High | Medium |
Surface Finish | High | Medium | High | Medium |
Production Volumes | High | High | Low | Medium |
Range of Materials | High | High | High | Medium-High |
Cost | Medium | Low | High | Medium |
Service:
1, 100% inspection before shipment.
2, Satisfied packing, carton, wooden case, pallet,or according to your requirement.
3, Samples are within 35-40 days after the receipt of the deposit. production will be finished about 25-30days after samples confirma
Production Capacity comparision of MIM and other process
Most difficult metals and compounds, pseudo alloys, porous materials can only be manufactured by powder metallurgy